The Mesh Mould project, developed by the Swiss National Centre of Competence in Research (NCCR) Digital Fabrication, is an innovative, sustainable construction method that uses robotic technology to create digitally fabricated metal meshes, eliminating the need for traditional timber formwork. Successfully implemented in the DFAB House in Dübendorf, Switzerland, it symbolizes the fusion of digital technology with traditional construction techniques, showcasing the potential for more efficient, accurate, and eco-friendly building processes while also pushing the boundaries of architectural design.
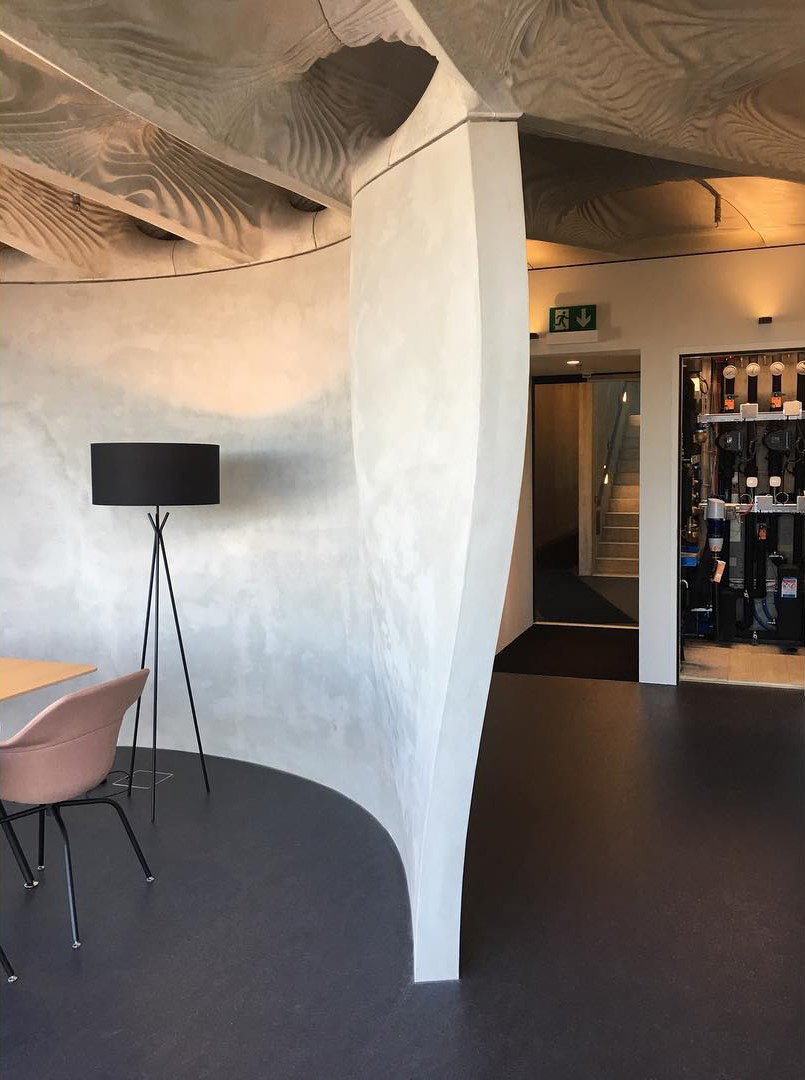
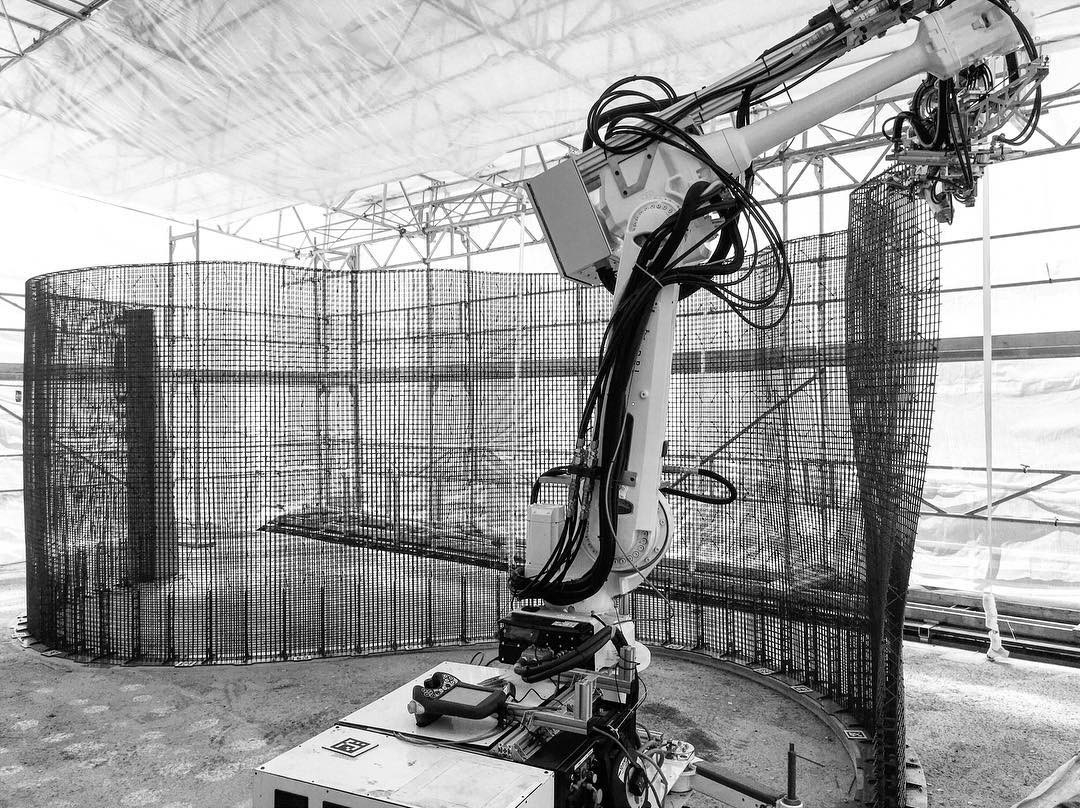
In the world of architecture and construction, innovation is a continuous endeavor. One such groundbreaking venture is the Mesh Mould project, as seen in the DFAB House in Dübendorf, Switzerland. This project is a testament to the application of cutting-edge robotic technology in the realm of construction and serves as a benchmark for sustainable and efficient building techniques.
The Mesh Mould project, developed by the Swiss National Centre of Competence in Research (NCCR) Digital Fabrication, is an innovative robotic fabrication method that marries the functionalities of formwork and reinforcement into one digitally fabricated metal mesh. This technique eliminates the need for conventional timber formworks, thereby introducing substantial efficiency, sustainability, and precision in the construction process.
Embedded within the DFAB House, the Mesh Mould technology was put to real-life testing and emerged as a triumphant pioneer in automated construction technology. The first ever load-bearing wall constructed using this process is situated in the DFAB House, a living laboratory for futuristic construction methods situated in the NEST building of Empa and Eawag.
The wall is a complexly curved concrete structure, showcasing not just the functional competence of the Mesh Mould technology, but also the aesthetic possibilities it brings forth. Despite its intricacies, the wall was robotically fabricated with a high degree of accuracy, thereby illustrating the precision that digital construction methods can deliver.
Furthermore, the environmental advantages of the Mesh Mould technology are considerable. By removing the need for disposable timber formwork, a substantial amount of construction waste can be prevented, driving the construction industry towards a more sustainable future.
The successful application of the Mesh Mould technology in the DFAB House signifies a monumental leap in digital fabrication in construction. It not only embodies the potential for more efficient, precise, and environmentally friendly construction processes but also opens up new vistas for architectural design that were previously unachievable.
Mesh Mould at the DFAB House in Dübendorf underpins the intersection of cutting-edge digital technology and traditional construction techniques. It is a beacon of inspiration for architects, engineers, and designers alike, as they navigate the path towards more sustainable and innovative practices in architecture.
Leading Researcher:
Prof. Fabio Gramazio - Gramazio Kohler Research, ETH Zurich
Prof. Matthias Kohler - Gramazio Kohler Research, ETH Zurich
Prof. Dr. Robert Flatt - Chair of Physical Chemistry of Building Materials, ETH Zurich
Prof. Dr. Jonas Buchli - Agile & Dexterous Robotic Lab, ETH Zurich
Prof. Dr. Walter Kaufmann - Chair of Structural Engineering - Concrete Structures and Bridge Design, ETH Zurich
Researcher:
Prof. Dr. Norman Hack (Project lead), Prof. Dr. Kathrin Dörfler, Julio Ramon López Alonso, Dr. Nitish Kumar, Dr. Andrew Lies, Dr. Timothy Wangler, Dipl.-Ing. Alexander Nikolas Walzer, Dipl.-Ing. Maximilian Seiferlein
NEST (Next Evolution in Sustainable Building Technologies): The NEST platform, a joint initiative by Empa and Eawag, provided the location for the DFAB House, serving as the real-world testing ground for the Mesh Mould technology.
Industry Partners: Various industry partners were involved in the project to ensure the technology's successful transfer from the laboratory to the construction site. These partners contributed materials, knowledge, and resources that were vital to the success of the project.
By working in synergy, these entities successfully brought the Mesh Mould project to life, marking a significant milestone in digital fabrication in construction and paving the way for future innovations in this field.